3 Reasons Your Mobile Maintenance Initiative May Not Be OSHA Compliant, and What You Can Do to Correct It
First and foremost, let’s be clear, OSHA—the Occupational Safety and Health Administration—doesn’t have current regulations directly addressing the use of mobile devices as a tool in the workplace.
But that doesn’t mean there are not potential pitfalls with your current iOS, Android, or other mobile device and applications.
OSHA exists to “ensure safe and healthful working conditions for working men and women by setting and enforcing standards and by providing training, outreach, education and assistance.”
Maintenance teams are no exception. Maintenance technicians and professionals are among a large group of employees who work in exceptionally dangerous conditions daily.
Safety and Health Program Recommended Best Practices
Under its mission to protect workers, OSHA has published a series of Safety and Health Program Best Practices. This document covers a full 36 pages of information, but can be summarized into the following seven (7) core focus areas:
(The complete guidelines can be reviewed here. A separate Best Practices for Construction is also available.)
1. Management Leadership – Organizations need buy-in from the top to put safety and continuous improvement at the forefront of all they do.
2. Worker Participation – Workers should be involved in creating, maintaining, and actively participating in a safety and health program. Any barriers or impediments to participation should be removed.
3. Hazard Identification & Assessment – Procedures and protocols should be established to identify and correct hazards and risks to employee safety. Routine inspections should take place, and any safety incidents should be investigated to determine the root cause.
4. Hazard Prevention & Control – Employers and workers cooperate to eliminate, prevent, or control workplace hazards. Plans to implement controls, monitor progress, and evaluate their efficacy should be developed.
5. Education & Training – All workers are trained on the program, their responsibilities, and how to identify workplace hazards. Employers, managers, and supervisors should all understand their responsibility for protecting workers’ rights and how to respond to reports and concerns.
6. Program Evaluation & Improvement – Safety programs should be continually evaluated and improved where needed.
7. Communication & Coordination for Host Employers, Contractors, and Staffing Agencies – All employees should be provided the same level of safety and communication regarding any hazards. Host employers should establish standards for contractors and staffing agencies.
With these core focus areas in mind, most organizations develop a robust written Safety and Health Program that will allow them to meet all the regulations and recommendations provided by OSHA.
OSHA even provides a helpful Safety and Health Program Audit Tool to ensure your organization’s plan will be successful and identify any deficiencies or areas of improvement.
So, How Does All This Impact My Mobile Maintenance Operation?
Well, to answer that, ask yourself this:
Does your mobile maintenance application allow you to successfully execute on OSHA’s Best Practices and your organization’s established Safety and Health Program?
If you answered with an affirmative “Yep,” then you are probably in the clear! Good to go!
If you answered “No” or, better yet, “I have no idea what the heck you are talking about,” read on.
Three Reasons Your Mobile Maintenance Application May Not Support Your OSHA Initiatives
Reason #1: It Doesn’t Provide Your Technicians All the Information
Mobile maintenance apps are on the rise for a lot of reasons. They can eliminate burdensome paperwork and can support organization-wide paperless and green initiatives. They can free maintenance technicians from a desk…or rather, the need for a desktop application. They can provide better collaboration, more efficient processes, reduce errors, and much more.
We even threw our hat into the ring, developing a unique mobile application for Oracle eAM customers, which significantly eases the transition from paper to mobile by mimicking your existing work orders.
But once you connect that mobile application to your ERP, you might start seeing some pitfalls. For many Oracle eAM and JD Edwards CAM customers, your critical work order attachments are embedded in the database as files or URL links. If this is the case, and your mobile application can’t effectively pull these files for your technicians in the field, you have a pretty big problem.
As part of your organization’s written Safety and Health Program, you likely have established requirements to share critical information about the asset, important safety information and checklists, and other important files like lockout tagout procedures.
If your mobile application can’t display those critical documents, your organization is falling behind on many of OSHA’s Best Practices:
- Management is not setting up staff to be successful;
- Workers don’t have the information to keep them safe;
- Hazard identification and assessment tools are not available; and, as a result
- Hazard prevention and control is completely lost.
Quick Fix: Ensure Your Critical Work Order Attachments Can Be Consumed on a Mobile Device
Adopting a solution that can access and read all your attachments, whether they are embedded in your ERP, saved to a SharePoint or Documentum library, or even stored in a network folder is critical.
But, even if your solution can find these files, iOS and Android don’t always play nice with image files, Word docs and Excel spreadsheets.
Regardless of your preferred mobile application, a solution such as AventX that can grab all the file attachments and convert them to a single file in a standardized format (PDF) is your best bet for ensuring critical safety information is accessible and legible on all mobile devices.
Reason #2: Safety Checklists and Other Procedures Can’t Be Marked Up and Signed
Now that your maintenance technicians are getting all those crucial documents through your mobile app or device, they have the information they need to tackle their assigned work. More importantly, the files are in an easy to consume format—PDFs that can be navigated through, zoomed in on, and quickly reviewed.
You can check off the “Management Leadership” and “Worker Participation” line items on your Safety and Health Program.
But are your technicians participating? You’ve provided them the files, but as of right now, the only thing they can do is look at them.
If all your technicians in the field can do is view the files, your leadership and management team may be missing the mark on possibly the two most critical components of OSHA’s Best Practices:
- Identify and assess hazards and dangerous situations; and
- Prevent and control these situations before they create problems.
Without the ability to “use” attached forms—checklists, signature approvals, etc.—the whole Safety and Health Program begins to unravel.
Leaders and managers lose control of the procedures that are in place to ensure safety. Workers can ignore these critical documents because there is no system in place to monitor how the documentation is being used.
Quick Fix: Ensure Your Critical Work Order Attachments Can Be Interacted with on a Mobile Device
So, your next step is to ensure that these mobile-ready files are interactive, making sure that they can be annotated, marked up, signed, stamped, and more.
Manually created PDFs can be set up to be saved with interactive elements, like checkboxes and signature panes. When saved back into Oracle eAM, these files can then be accessed from the database by some mobile applications.
AventX for Oracle eAM’s Digital Print feature extends AventX’s attachment-gathering capabilities by saving a copy of the complete work order packet back to the Work Order header.
This provides a complete work order with all its attachments available to any mobile maintenance application that can view the work order header. More importantly, the AventX solution maintains any interactive functionality of PDF attachments.
By providing technicians with the tools to interact with your work orders and, more importantly, the safety documentation that comes along with them, your organization has the tools to maintain a safe and productive working environment.
Reason #3: Single Source of Truth for Program Evaluation and Auditing
At this point, we’ve reviewed the importance of 1) providing all the safety (and other) documents via a mobile application and 2) the ability of technicians to interact with those documents.
But you may still be missing out another critical Best Practice that may leave you open to potential OSHA compliance issues.
That is the Program Evaluation & Improvement component.
For organizations running a successful Safety and Health Program, there should be a single source of truth for evaluating the use of safety checklists and documentation. Leaders and managers need the ability to monitor the use of these all-important forms periodically.
Moreover, you may, at some point, need to show these documents to officials should you ever undergo an OSHA audit.
While the right file type (PDF) and annotation capabilities of many mobile maintenance applications provide much of the needed infrastructure to be successful, they often can’t distribute these necessary documents, once completed, to a final destination. This is especially true for organizations running Oracle eAM with a third-party application, which often don’t send completed documents back to the eAM module.
These files need a final resting place for leaders and managers to track progress and discover areas for growth.
Quick Fix: Ensure Marked and Signed Documents are Saved to a Single Location
Ensuring that your mobile application can save completed work orders and their safety documents back to a central location is critical.
Leaders must have the ability to monitor employee usage and manage to deficiencies. For many organizations, this single source of truth is Oracle eAM itself.
If your mobile application cannot save the document back to Oracle or to an external library, like SharePoint, you may be setting yourself up for disaster.
To supplement third-party applications, the Digital Print feature of AventX can make these critical files accessible from your networked libraries for both initial usage and for archival or auditing purposes. Or, the AventX Mobile for Oracle eAM application easily saves these documents back to the work order in Oracle eAM.
In Review
Mobile applications are undoubtedly the future of the maintenance industry. However, there are three key areas that may present challenges for organizations, especially when it comes to OSHA Best Practices and compliance.
- Missing or incomplete information making it to the field
- Critical safety sheets and checklists that are not interactive
- No mechanism available for program evaluation and auditing
For organizations to execute effective Safety and Health Programs in support of OSHA’s mission, they must review the available Safety and Health Program Best Practices and the Safety and Health Program Audit Tool.
Organizations must also understand and document the role of maintenance applications as they relate to established safety programs. If your maintenance application is deficient in even one of the three areas above, you may be opening the company to violations and fines.
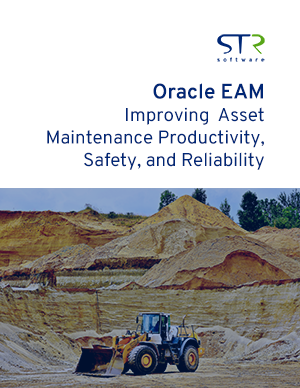
White Paper
Improving Asset Maintenance Productivity, Safety, and Reliability
For maintenance organizations running Oracle E-Business Suite Enterprise Asset Maintenance (eAM), a functionality gap that users commonly recognize is the inability to print work orders with their associated attachments. In asset-intensive industries, maintenance departments bear the burden of ensuring the reliability of aging equipment. The key to keeping up with asset reliability is scheduling preventative and corrective maintenance, and providing maintenance crews with the documentation they need to be safe and successful at their jobs.
Plus, learn about AventX’s Digital Print feature in the Spring 2020 Release Summary.
Contact us for a demonstration »